Optimising fleet operations with Shell Sarnia - MachineMax solution pays for itself
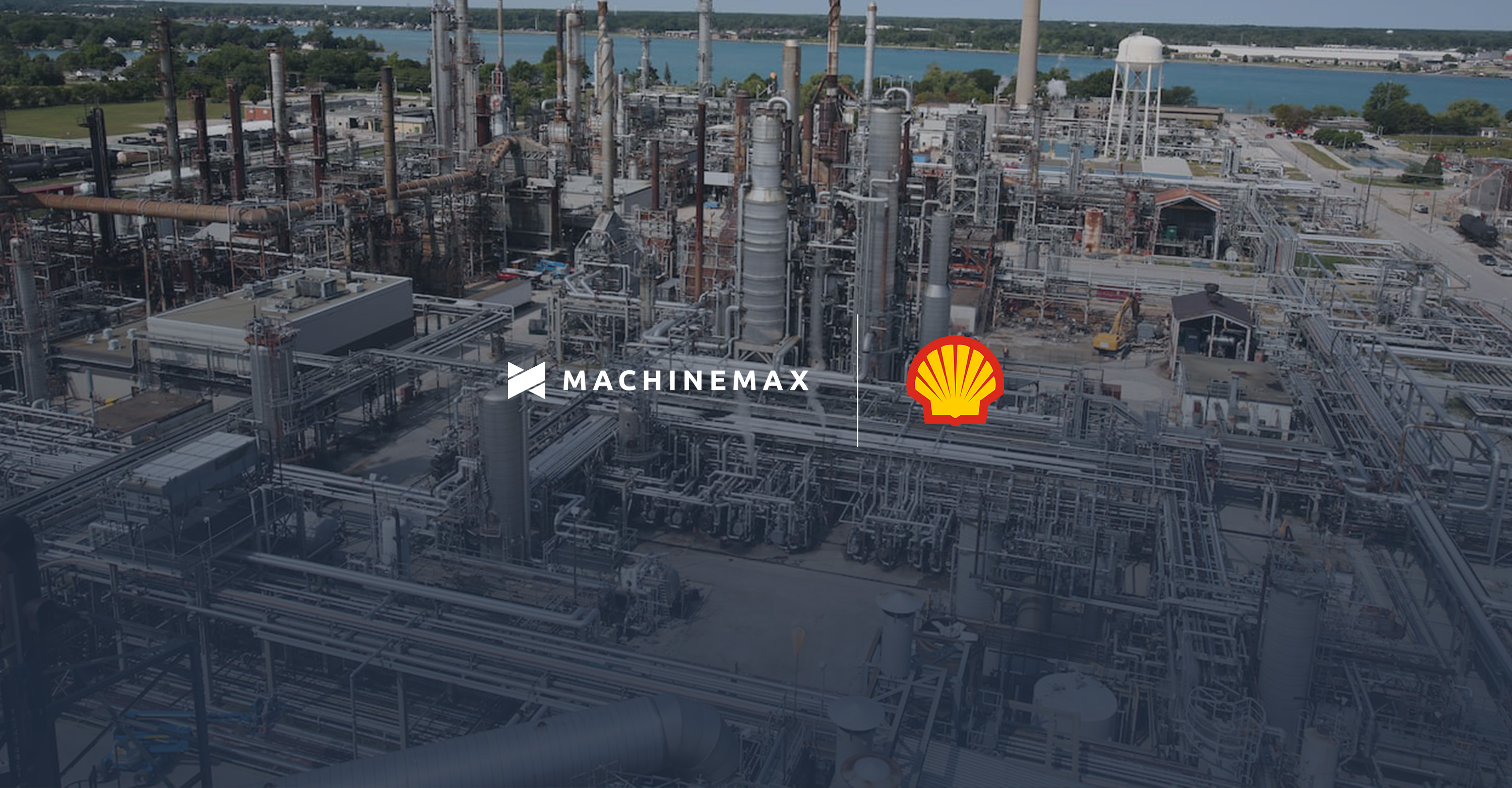
The project:
- Associated company: Shell Canada Limited (subsidiary of Shell plc)
- Location: Ontario, Canada
- Machines: 100
- Site acres: 540
The challenges:
The Sarnia manufacturing centre previously had no means of collecting any data on idling, utilisation, hours worked and emissions. This meant that it was hard to identify bottlenecks in their fleets operations which meant that they couldn’t refine and optimise their site.
Not only that, by not having access to idling and emission data it meant that they firstly found it hard to report on emissions but secondly, they couldn’t actively try to reduce their fuel consumption by attempting to reduce idling.
The solution:
To tackle these challenges Shell Sarnia trialled the MachineMax system which provided them with much-needed data such as real-time GPS, idling, utilisation ect.
After expanding the integration for the entire site, the team managed to identify several inefficiencies such as excessive idling and low utilisation on some machines. This allowed them to either remove or reassign underutilised vehicles allowing them to cut costs and make better use of the machines they did have.
Shell Sarnia's data analysis pinpointed inefficiencies, enabling strategic changes that boosted efficiency. The implemented improvements have not only covered the MachineMax system costs but also positioned the facility for sustained success.
Testimonial:
"By taking the first five vehicles out of the fleet and reallocating around ten others the MachineMax platform has already paid for itself for the next five years, and it has only been four months”
Jason Kimball - Maintenance, Construction and Turnaround Manager at Shell Sarnia.
Click below to dive into the full case study: