MachineMax Streamline Forterra with Fiix
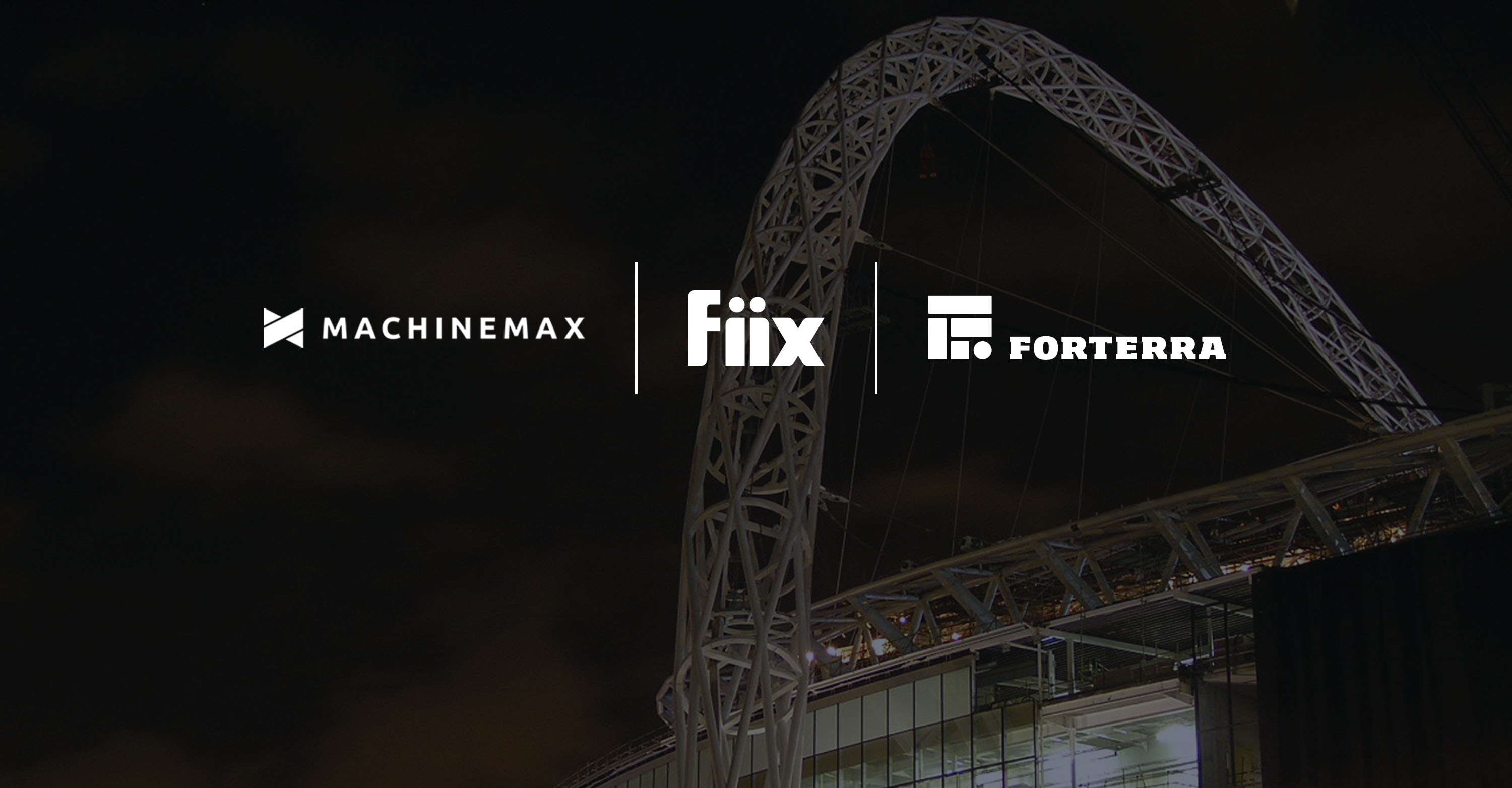
For the past 2 years, MachineMax and Fiix have partnered to successfully connect heavy equipment telematics and maintenance. The partnership has seen the two software providers integrate data from onboard telematics with CMMS software. The integration between MachineMax and Fiix has enabled decisions to be made in real-time, using the most up to date and accurate data. These data-driven decisions have improved machine reliability while decreasing maintenance expenditure.
The joint offering has helped customers digitalise their fleets and the respective maintenance processes, eliminating paper-based tasks and manual data inputs. Making data driven decisions on maintenance minimises the risk of over or under maintaining equipment. This leads to improved scheduling accuracy and thousands of dollars saved in breakdowns, as a result of incorrect maintenance. This automated process is scalable, ensures real-time insights, eliminates human error and reduces admin time and costs.
“By tapping into advanced Industry 4.0 capabilities, teams will be able to capture quality data, put best practices into place, improve asset performance and save money,”
says James Novak, CEO of Fiix.
Forterra is one example of a Fiix customer that has seen success from the partnership. Forterra builds sustainable infrastructure through strategically located facilities in the United States as well as in Mexico and Eastern Canada. Since setting their foundation in 1899, they have evolved dramatically in the areas of distribution, technology, and product development – not only to move water, but to employ its benefits for sustainable communities.
As a result of their success with Fiix, Forterra realised they needed to integrate MachineMax into their off-road equipment to bridge the gap between machine reliability and maintenance expenditure. Forterra were firstly interested in the MachineMax’s ability to measure the real-time working hours of their equipment. As they previously had the challenge of logging this manually which was which was time consuming and expensive. Logging this digitally enabled Forterra to understand the downtime, productive hours worked and when the machines are not working on an integrated, simple to use platform.
In spite of the real-time hour-metre being the initial feature that attracted Forterra, they realised they could get more out of the partnership between Fiix and MachineMax. Therefore, through the platform they started to measure real-time utilisation data which can be integrated into a CMMS. Having real time utilisation allowed visibility on patterns in operational inefficiencies including: too many equipment onsite resulting in under-utilisation, incorrect equipment used for the job resulting in lower productivity, ineffective site layout resulting in idling and excessive travelling, suboptimal operator behaviour resulting in dangerous, and inefficient utilisation.
Jay Hampton – Forterra Director of Maintenance says:
“MachineMax allows for visibility of our fleet regardless of the brand at every level of the organization. The value for me is to focus on utilizing the fleet to prioritize resource allocation. This platform helps me drive sustainability goals aligned with the community we live in.”
Through this collaboration MachineMax and Fiix have been able to alleviate manual processing, increase machine reliability and reduce maintenance expenditure all whist increasing the utilisation of Forterra’s operations and machinery.
Creating value and making customer’s lives easier is what this partnership was intended to achieve and we are pleased to see it paying dividends.