MachineMax: constructing the connected site of the future
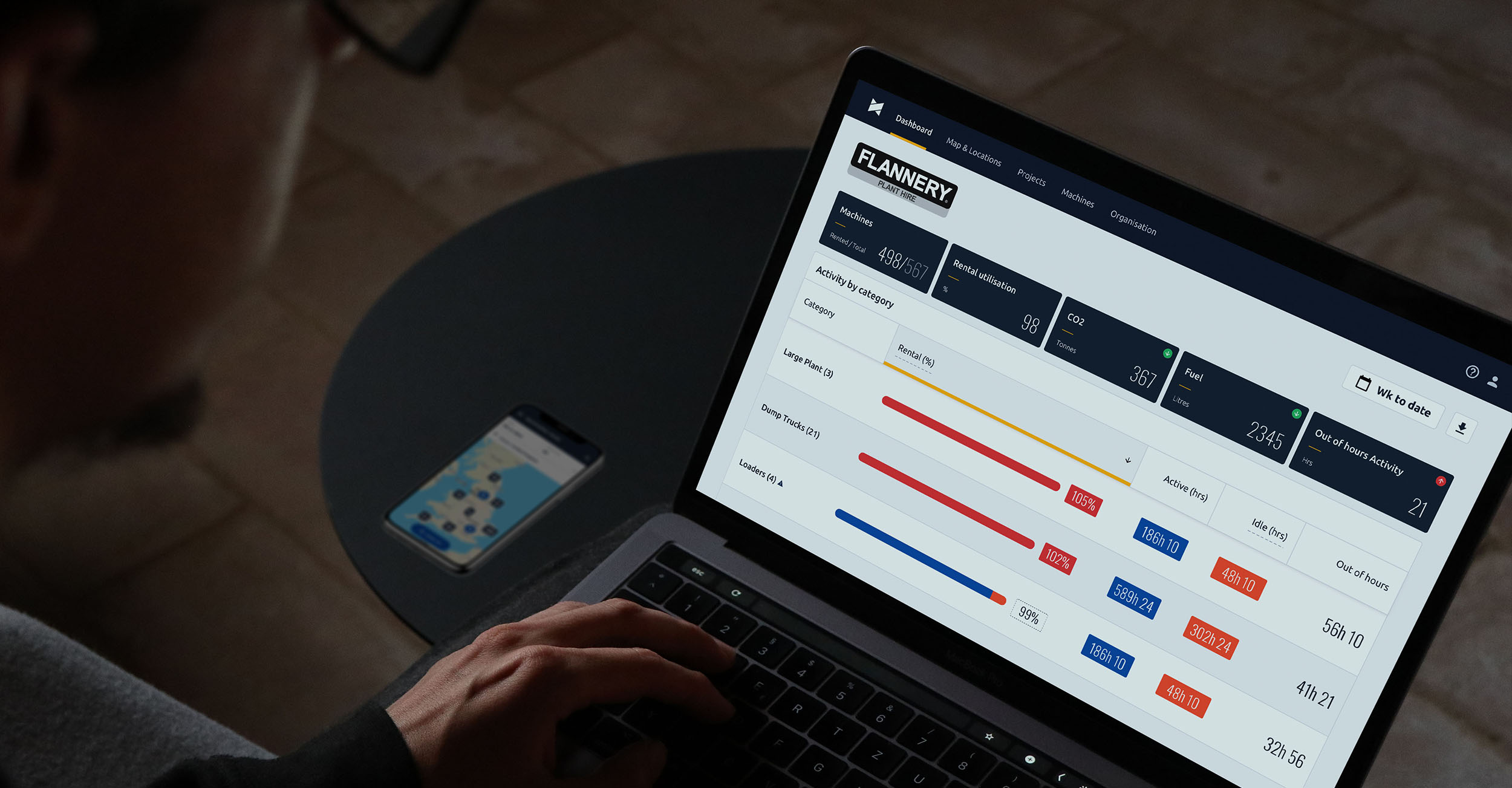
It is an undeniable fact that understanding exactly how a fleet is being used is the first step to greener and more productive construction and infrastructure projects. As these industries become more target focused, delivering a more sustainable project solution (with data to prove it) is increasingly important.
As a business, we constantly challenge ourselves to provide the most innovative and sustainable solutions to our clients. Together with MachineMax, the Flannery team have created a focused case study explaining the Flannery telematics solution and identifying best practise in utilising the technology. This solution allows Flannery clients to remotely manage their entire fleet, to support a reduction in operating costs and to make proactive decisions in real-time to drive value and sustainability best practise.
Having insights into real-world utilisation empowers plant managers with accurate data, allowing them to evaluate the machine mix on site and if the fleet is working at its optimum capacity. In addition to this, the data can provide excellent information on operator performance, identifying training opportunities and driving positive behavioural change onsite.
With the right analysis, the biggest areas for improvement come by making small operational changes ensuring the impact of idling & emissions can be minimised.
Read the case study to find out more about the new telematics dashboard in action.